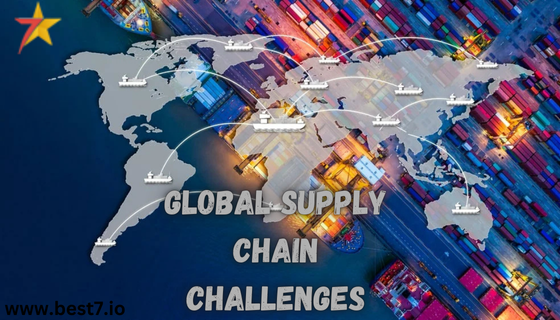
These disruptions to global supply chains have been felt across the modern automotive landscape and are continuing to play out in the production and sales of vehicles worldwide. The complex supply chain of suppliers, producers, and logistic providers has struggled on numerous fronts with external influences. That is having major and widespread effects on automotive production in the midst of related market challenges and poses a clear danger for the industry.
Globally, Understanding the Challenges in the Supply Chain
The automotive industry has traditionally looked to leverage a world-spanning supply chain for the efficient provision of both materials and components. Although, global events like the COVID-19 pandemic and natural and geopolitical adversities that occurred recently have exposed a major flaw in the predominance of these supply chains. The World Economic Forum found that 94% of Fortune 1000 companies had experienced supply chain problems because of the disease, as noted by IHS Markit in their Online Purchase Managers Index. Even auto makers are not immune from these pressing problems as this staggering number makes clear.
Material Shortages in the Automotive Industry
Material Shortage: One of the biggest challenges facing the automotive industry today is a material shortage. Across the board, factory shutdowns from the pandemic caused slowdowns in production as manufacturers work to catch up on back orders. Add a global shortage of semiconductors that has hurt car production, and the long list of reasons folks aren’t opting for the electric life becomes apparent.
Semiconductor Shortage: A Major Roadblock
Semiconductors are the modern engine of most vehicles, controlling everything from infotainment systems to advanced driver-assistance capabilities. IHS Markit reports that the global semiconductor shortfall will lead to a shortfall of 7.7 million cars this year alone. As a result, automakers had to stop their production lines resulting in huge delays and monetary losses.
Rising Material Costs and Inflation
Another issue has been the price hike that many materials faced. The prices of metals such as steel and aluminium have soared on rising demand and supply-chain disruptions. The American Iron and Steel Institute says steel prices from early 2020 until mid-2021 climbed 150%. They have put pressure to reconsider their pricing strategies and production plans for manufacturers.
Logistical Delays Disrupt Automotive Operations
Another major factor to hinder the production and sales of vehicles is logistical delays. A pandemic breaking out all over the world causing wide-ranging disruption of transport networks has proved to be a major chokepoint in goods movement.
Port Congestion and Its Impact
West Coast ports in the United States and other major ports have been impacted by a congestion of shipping containers. An NPR report said a study funded by the Pacific Merchant Shipping Association found container ships waiting to unload at the Port of Los Angeles had spiked by 500% compared to pre-pandemic amounts. All of this gridlock has played into slowing down the arrival of critical components required for manufacturing.
Fast-Rising Shipping Prices
Soaring transportation demand in conjunction with constrained capacity has driven transport costs through the roof. Freightos says shipping a container from Asia to the U.S. went from around $2,000 in early 2020 to more than $20,000 by the end of 2021. The increased shipping fees affect the price of cars across the board, because this becomes a new operating sanction by manufacturers.
Production Bottlenecks in Automotive Manufacturing
Production bottlenecks have been routine as automakers grapple with material shortages and logistics delays. By unplugging these bottlenecks, disordered manufacturing is in place and reducing output.
Assembly Line Shutdowns
Assembly lines have paused across many as manufacturers experience stoppage in the flow of critical components. For example, Ford and General Motors said they would stop making some vehicles at a number of plants because of semiconductor shortages. That mixed with the coronavirus pandemic-declared federal emergencies we endured actually resulted in a 20% decline in vehicle production overall during Q1 and Q2 2021 over 2020, according to Automotive News.
Workforce Disruptions
Work disruptions have also resulted in the disruption of workforce within the automotive industry. As the production lines have slowed down, manufacturers have had to adjust their staffing levels and shift schedules, leaving employees wondering what will come next. All that does is make it harder to bounce back from the recovery as if we need another challenge in workforce management.
The Impact on Automotive Sales
Supply chain disruptions revise the course of automotive sales by more than just affecting production. With consumers now facing a shrinking pool of vehicles, the market dynamics are changing.
Decreasing Sales Numbers
With the decrease of roughly 3.9%, U.S. new vehicle sales in 2021 totaled around 15.3 million units based on Cox Automotive. The drop was blamed on production delays and shortages as dealers faced a shrinking inventory of vehicles to offer consumers.
Changes in Consumer Behavior
With consumers becoming more careful about their purchase, the preference has shifted. Buyers looking to replace their old vehicle, however, have fewer options and have continued to turn to the used car market where there is still more inventory available. This adjustment has now led to a spike in demand for secondhand cars, leading to higher prices and intensified buyer competition.
Long-Term Implications for the Automotive Industry
These global supply chain challenges will no doubt have long-term impacts on the auto industry and shape strategy and operations for years to come.
Investments in Supply Chain Resilience
Automakers are likely to make significant investments towards more resilient supply chains so as to not get entangled in future turmoil. This could include diversifying suppliers, stocking up on inventory, and deploying supply chain management tools using state-of-the-art technology. According to a McKinsey report, companies investing in supply chain resilience could easily lead to a 15% incremental growth more than their peers.
Shift to Local Sourcing
The pandemic has not only exposed the risks associated with global supply chains, but has pushed for discussions around local sourcing. Automakers can reduce this risk by partnering with regional suppliers to reduce their dependence on international logistics.
Automotive Production Innovations
In response to these changes facing the automotive sector, revolutionized production processes and technologies are keener than ever.
Rise of Industry 4.0
Incorporation of Industry 4.0 technologies, such as automation, AI, and big data analytics to drive enhancements in production efficiencies; reduce dependency on conventional supply chains. Manufacturers can use these technologies to streamline their operations and be more agile in a world where the consumer preference can change on a dime.
Focus on Sustainability Initiatives
Another key factor that will play a significant role in the future of automotive production is sustainability. With consumers increasingly opting for eco-vehicles, the idea is stable that automakers will have to embrace sustainable business practices. This can include supporting green tech, embracing the circular economy, and developing more sustainable manufacturing.
What the Future Holds for the Automotive Industry
While we cannot predict the future, it is almost inevitable that the automotive sector as a whole will see transformations few of us had gotten to experience (both in good and bad ways). Manufacturers who adapt and overcome will navigate these perilous waters — and come out the other side stronger.
Collaboration and Partnerships
Meticulous work is required among automakers, suppliers, and technology providers to solve supply chain challenges. These key stakeholders can collaborate, pool resources, share information and best practices to drive increased efficiencies — building more sustainable supply chains for the success of all.
Consumer-Centric Approaches
Being consumer-centric, the automobile industry needs to be agile and responsive since consumer tastes are moving targets. When manufacturers prioritize the needs of their customers, and streamline purchasing for better purchase experiences, this ultimately helps to secure trust and loyalty with consumers.
Preparing for the Future
Global supply chain disruptions have a deep influence on the automotive sector, triggering production delays and sales and market developments. As the industry faces these dynamics, automakers are expected to look for different approaches to achieve innovation, invest in resilience, and drive sustainability. The automotive industry can prepare itself for the future and the new trends by better understanding the current landscape.